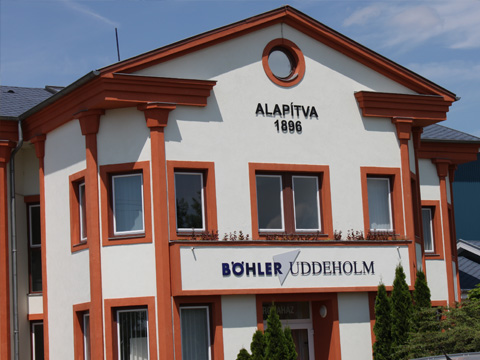 | Böhler Uddeholm – tool stell speacialist |
---|
Böhler Uddeholm Hungary is a memeber of a famous VOESTALPINE AG group with a headoffice in Linc, Austria. BOHLER-UDDEHOLM Hungary Kft was founded in 1986. The production in Hungarian is focused on machining of wide range of workipices. The expansion of production has created a need to purchase new technologies for precision turning, grinding and grooving.
|
|
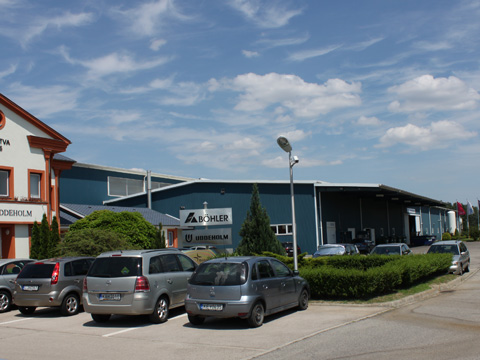 | Uddeholm tool steel in your everyday life |
---|
You'll find Uddeholm steel in cars, mobile phones, consumer electronics or anywhere where high accuracy and optimum performance is required. For example, toothbrushes ORAL are made of Uddenholm tool steel. This steel can also be found in most of the high quality cars (engine blocks, door beam or a dash board).
|
|
|
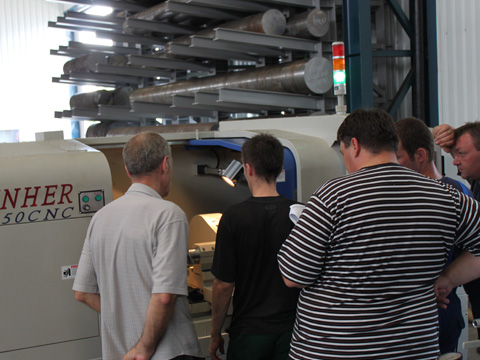 | Training and sample grinding on the JHI 150 CNC grinding machine |
---|
The operation and programming of the internal grinding machine JHI 150 CNC is very easy. The grinding machine has built-in macros for different types of operations. It´s just necessary to understand the principle and set the grinding parameters afterwards. The training in the company Bohler took 2 working days and the next day the operators were able to produce complete pieces.
|
|
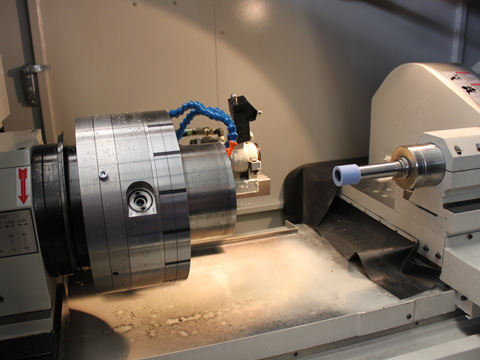 | JHI 150 CNC equipped with hydraulic chuck and magnet |
---|
Not every workpiece can be clamped in the chuck. For this reason we additionally had to mount a permanent magnet from the Czech manufacturer WALMAG on the machine. It takes less than 20 minutes to change the magnet and the hydraulic chuck, including the workpiece and magnet centering.
|
|
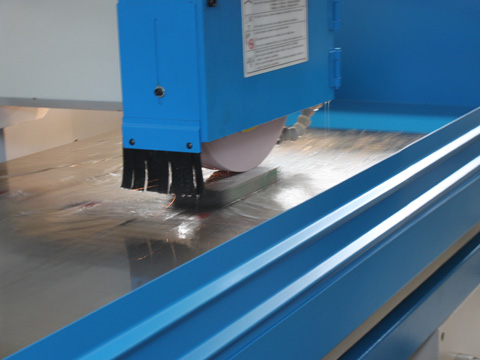 | Sample grinding on the PROTH - PSGO 75150 AHR grinding machine |
---|
The PSGO 75150 AHR grinding machine has been delivered together with the AD1 system which allows to perform grinding cycle automatically without operator’s intervention. Grinding of this workpiece was really a piece of cake.
|
|
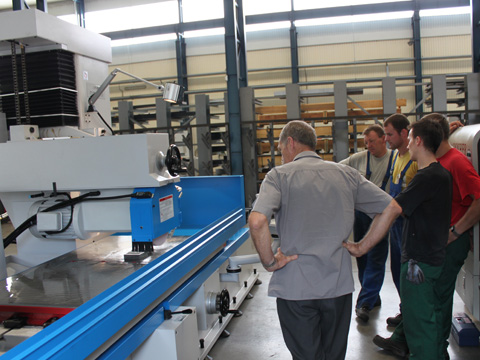 | How long does it take to train an operator for PSGO 75150 AHR? |
---|
The operators fully understood all the functions and settings of the automatic grinding cycle in two hours. Due to the failure of the customer’s older grinder the production started immediately after the training.
|
|
 | Equipment of the PROTH - PSGO 75150 AHR surface grinding machine |
---|
Electromagnetic table 750 x 1500 mm with an automatic demagnetizer, automatic grinding cycle AD1, variable spindle speed, magnetic separator + paper filtration, easy to set the range of the cross traverse through an electric button, the grinding wheel 355x50x127 mm, dressing attachment mounted on the table, 2V guide ways in the traverse and longitudinal axis, criss-cross grinding function, automatic lubrication system.
|
|
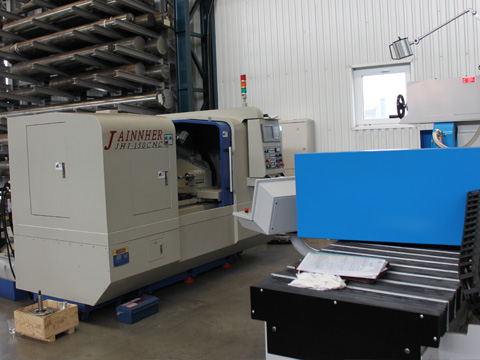 | Equipemnt of the internal grinding machine |
---|
Fanuc control system, internal grinding range 6-150 mm, spindle speed of 10,000 rev / min., automatic controlled dressing equipment, magnetic separator + paper filter, hydraulic chuck (o 200 mm), WALMAG permanent magnet (o 400 mm), full cabin covers.
|
|
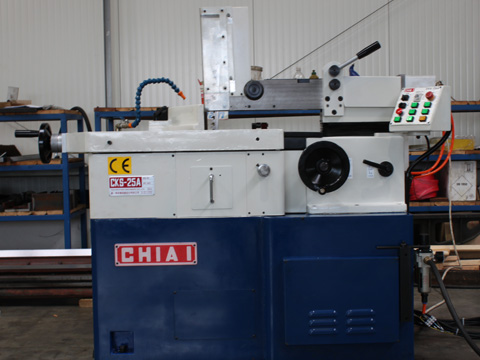 | Efective production of slots -Keyseater CKS 25A |
---|
Keyseater CKS 25A was the third supplied machine. In comparison to the shaping machine with one edge, this machine has several tool cutting edges. This makes the cutting groove more productive and the surface appears to be better than on conventional machines. On this machine you can effectively cut grooves of size 3-25 mm.
|
|
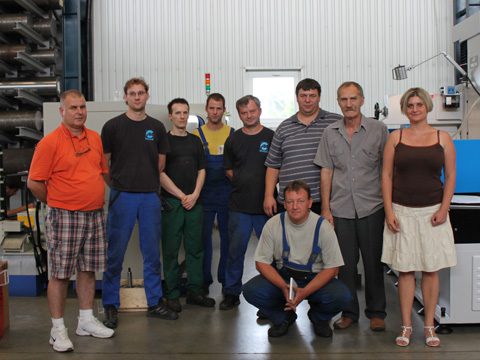 | The customer’s satisfaction with the delivered machines has lead to a further cooperation |
---|
In the presence of a production manager Mr. Bologh (on the left) and our representative Mr. Fehervariho (second from the right) all three machines were duly taken into use on 17th July 2013. During the whole process a promise for further cooperation has been made – namely a supply of the PROTH double column grinder.
|
|